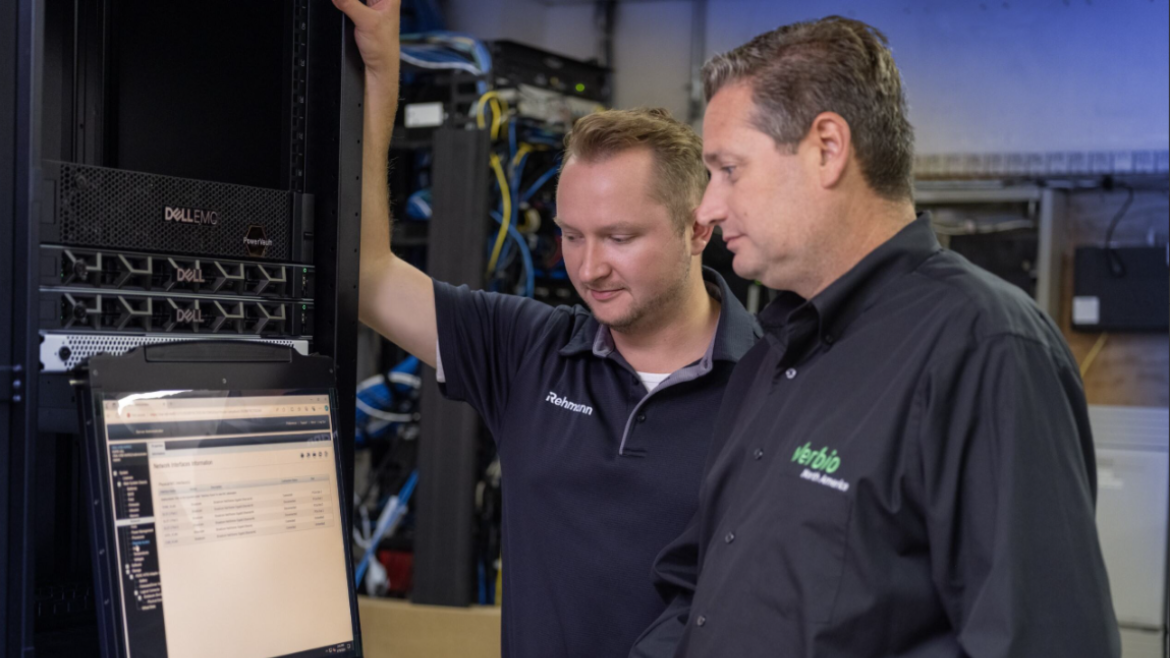
For the last quarter century, smart manufacturing has reshaped the way manufacturing works. Those of us who have led shop floors into the new millennium will remember a time when lean manufacturing and the standardization and specialization of processes, components, and tasks were the keys to improving efficiency and reducing costs.
But the meteoric rise of smart manufacturing — essentially, the use of interconnected technologies to create a flexible, efficient, and highly automated production environment — has pushed many manufacturers forward, faster.
Smart Manufacturing’s Piece of the Pie
Statistica reports that the market size of smart factories in the United States increased nearly 60 percent in the last 5 years alone, from $153.7 billion in 2019 to $244.8 billion in 2024.
This increase comes as multiple core technologies have been integrated into the manufacturing space, enabling manufacturers to reduce waste, cut costs, and streamline more processes, from production and supply chain management to predictive maintenance and quality control.
Who is — or Feeling — Left Behind?
Despite the rapid increase in market size, a global study of more than 1,300 manufacturers across 13 of the leading manufacturing countries found that, as of 2023, only a little over 40 percent of manufacturers have implemented smart manufacturing technologies.
Whether they have or haven’t implemented smart manufacturing technologies, many manufacturers suggest they’re feeling increasingly left behind in the smart-tech race: The same study found that twice as many manufacturing leaders in 2023 believe their organization lacks the technology needed to outpace their competition, as compared to 2022.
Where do you stand? Is your plant keeping pace with the latest and greatest in smart manufacturing technology? Sticking to the tried-and-true traditional manufacturing that’s served you (and perhaps previous generations) well? Or are you taking slow and steady steps toward adoption on a case-by-case basis?
Smart Tech’s Biggest Bangs for a Manufacturer’s Buck
Whatever your approach, it’s worth knowing the smart technologies that a recent survey of manufacturers reported as delivering the highest ROI within the last year. We’ve gone one step further, whittling down that list to highlight the five most accessible, affordable, and/or easy-to-implement smart technologies of the bunch — and how they could benefit your operation.
1. Cloud Computing
By moving their data to the cloud, manufacturers can eliminate the need for physical servers and data centers on-site. This frees up valuable floor space; transforms the upfront investments previously required for hardware, software, and other IT infrastructure into monthly or annual subscription costs that can be scaled up or down with usage; and reduces operational costs for maintenance, energy use, and IT staffing.
Bonus: Because cloud service providers invest so heavily in security measures, manufacturers who switch to cloud computing often enjoy better data protection, disaster recovery plans, and compliance and regulation adherence at far less cost or effort than they could in-house.
Want to know the first-hand experience (and savings) a company with 60 years of data and more than 100 employees had when it switched to the cloud? Click here for the story.
2. Automation and Robotics
Automation technologies, including collaborative robots (aka cobots), have been widely adopted to perform repetitive tasks, improve quality and consistency, and increase productivity. But cobots, in particular, tend to be a popular option for smaller manufacturers because they cost less than industrial robots, with lower upfront and operating costs.
Another perk: Cobots can easily be reprogrammed for different tasks, from physically demanding efforts like packaging and palletizing to more precise applications like component assembly. Their adaptability, affordability, compact size, and ability to enhance productivity — especially with difficult or repetitive tasks that can wear down their human counterparts — make them a great fit for small or mid-sized manufacturers short on space and workers.
3. 5G
If connectivity defines smart manufacturing, 5G technology is redefining it, enabling faster data transmission speeds than any generation before. Likewise, 5G has reduced latency — the delay between the moment you initiate a transfer of data and the moment it begins to transfer — to as little as 1 millisecond, a massive drop from 4G’s estimated 30-70 milliseconds. This means that data can be sent and received almost instantaneously, crucial for remotely controlling machinery and processes in real-time, as well as enhancing precision, productivity, and safety.
4. Enterprise Resource Planning (ERP)
An integral part of smart manufacturing, ERP systems help integrate and manage various business processes. Their superpower: Giving manufacturers a unified view of operations by consolidating data from different departments — think: production, supply chain, finance, human resources, etc. —into a single platform.
When used to their potential, modern ERP systems can provide a breadth of data and insights manufacturers can use to optimize processes, reduce waste and defects, improve efficiency, monitor and manage quality control, and — when integrated with other smart technologies — enable predictive maintenance to minimize downtime and extend the life of plant machinery and equipment. Ultimately, the integrated, real-time data that ERP systems offer empowers manufacturers to make more informed strategic decisions and enhance the overall performance of their business.
Have an ERP system but think it’s not working as you need it to — or considering an upgrade? Read The Manufacturer’s Guide to ERP Optimization and Selection first.
5. Artificial Intelligence (AI)
The field of AI is enormous and expanding at such a clip that giving more than a glimpse of its applications in manufacturing alone is near impossible. Suffice it to say that traditional, or “narrow,” AI, which relies on predetermined rules and algorithms to perform specific tasks and provide insights, is well-established in manufacturing, especially in conjunction with machine learning.
But Generative AI goes leaps and bounds further. It’s moving manufacturers beyond reactive applications, like analyzing machinery sensor data for more accurate prediction of equipment failure and maintenance needs, to proactive applications, where it learns from data patterns to generate new content and outputs.
Among Generative AI’s impactful uses we’re seeing in manufacturing today:
- Product Design and Prototyping: Generative AI can create thousands of design options based on specific parameters, allowing engineers to quickly evaluate and refine prototypes.
- Process Optimization: By simulating various production scenarios, generative AI identifies bottlenecks and suggests real-time adjustments to improve efficiency, ultimately reducing energy use, optimizing human resources and workflows, and boosting overall productivity.
- Supply Chain Optimization: Generative AI optimizes supply chains by forecasting demand, analyzing logistics, and recommending optimal inventory levels.
- Materials Optimization: Generative AI can analyze multiple materials and factors of each — think: cost, performance, and sustainability, and more — to help manufacturers select the best, most efficient, and cost-effective options available.
- Factory Layout and Workflow Design: Generative AI can design optimal factory layouts, simulating different configurations and material flow patterns to optimize available space, production efficiency, and overall workflow while minimizing operational costs.
While no single smart manufacturing technology is universally suitable, it’s certainly worth evaluating various options that can be tailored to your specific plant needs and circumstances. Prioritizing the exploration of different technologies can unlock significant benefits, helping you overcome staffing or downtime challenges, or reach specific goals for efficiency and product quality. Stay open to diverse solutions, and you’ll be better able to identify the most effective smart manufacturing tools for your business.