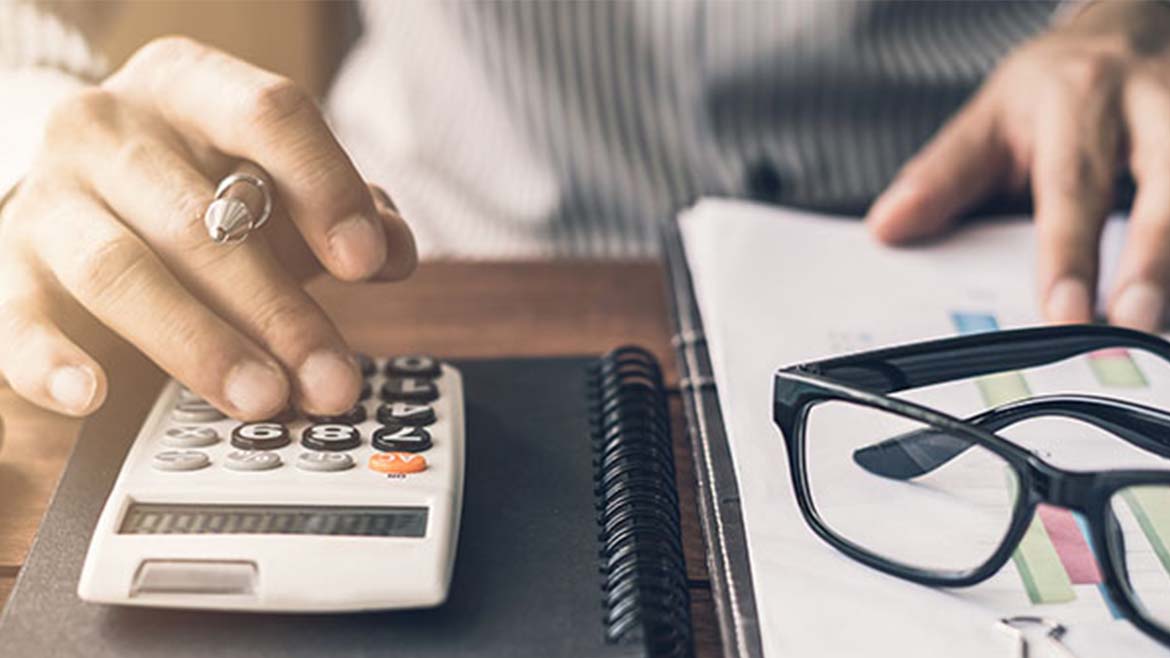
How financial data is collected and analyzed directly impacts a business’s operational efficiency and strategic decision-making. Lean accounting is a modern alternative to traditional cost accounting that aligns financial reporting with lean production principles. Here’s an overview of how these principles may help lean manufacturers streamline operations, reduce waste and gain more timely, meaningful financial insights.
Key principles of lean accounting
Competition and pricing pressures have forced many companies to adopt lean (or just-in-time) manufacturing models. Lean manufacturing is a “pull-demand” system, where customer orders jumpstart the production process. Lean companies view inventory not as an asset but as a waste of cash flow and storage space.
Lean accounting is a financial management approach designed to support lean enterprise principles. Instead of relying on complex overhead allocations and standard cost variances, lean accounting simplifies reporting. It focuses on real-time data, value-stream costing and continuous improvement. The core goals are optimizing resources and maximizing value for customers. (See “Standard cost accounting vs. lean accounting at a glance” below.)
COGS in lean accounting
A major advantage of lean accounting is improved traceability of the cost of goods sold (COGS). It assigns costs based on actual production activities rather than predetermined overhead allocation rates. Lean accounting methods divide production costs into four value-stream categories:
- Material costs,
- Procurement costs,
- Conversion costs, such as factory wages and benefits, equipment depreciation and repairs, supplies, and scrap, and
- Occupancy costs.
This method clearly shows the direct costs associated with production by grouping costs according to value streams rather than individual products. It ensures that COGS calculations reflect the real expenses incurred rather than being influenced by arbitrary allocation formulas. Because lean production emphasizes reducing excess inventory, COGS calculations become more accurate as they rely on lower inventory levels and shorter production cycles.
Additionally, lean accounting measures costs in short, frequent intervals rather than waiting until the end of a financial period. This period-based costing approach enhances transparency about production expenses and allows for more agile financial management.
Box score reports are often used in lean accounting to supplement income statements. These reports list performance measures that traditional financial statements neglect, such as scrap rates, inventory turns, on-time delivery rates, customer satisfaction scores and sales per employee. Many companies also swap standard cost accounting metrics with lean-focused key performance indicators, such as inventory turnover, order-to-cash cycle time and overall value-stream profitability.
Beware of the financial reporting effects
When a company first applies lean principles, the amount of inventory reported on its balance sheet typically decreases significantly. Why? The company must write off obsolete items and deplete in-stock inventories before producing more units. Often, companies discover that their inventories were actually overvalued in prior periods due to obsolete items and inaccurate overhead allocation rates (traditionally based on direct labor hours).
During the transition phase, several costs — such as deferred compensation and overhead expense — move from the balance sheet to the income statement. As a result, lean manufacturers may initially report higher costs and, therefore, reduced profits on their income statements.
From a benchmarking standpoint, liquidity and profitability ratios decline when traditional accounting methods are applied to newly improved operations. Alone, these financial statement trends might raise a red flag, but don’t let the numbers fool you. Standard cost accounting rewards inventory stockpiles and high machine use rather than increased capacity and waste reduction.
Supplementing GAAP reports
To comply with Generally Accepted Accounting Principles (GAAP), most companies stick with standard cost accounting for external financial reporting purposes. However, managers who review traditional and lean accounting statements in tandem are better equipped to understand the benefits of lean production and identify areas to target with future improvement initiatives.
Applying lean accounting methods requires significant changes in systems, processes and employee training. Contact your CPA to conduct a lean accounting readiness assessment and train your accounting team on value-stream-costing methods.
Sidebar: Standard cost accounting vs. lean accounting at a glance
Traditional standard cost accounting is deeply ingrained in financial reporting but often creates inefficiencies when applied to lean operations. Here’s how lean accounting compares:
Traditional cost accounting was developed for mass production environments, where large inventories and long production cycles are the norm. However, in lean organizations, these outdated costing methods can distort profitability analysis, leading to poor strategic decisions. Lean accounting removes these distortions and provides financial insights that align with lean principles.
© 2025