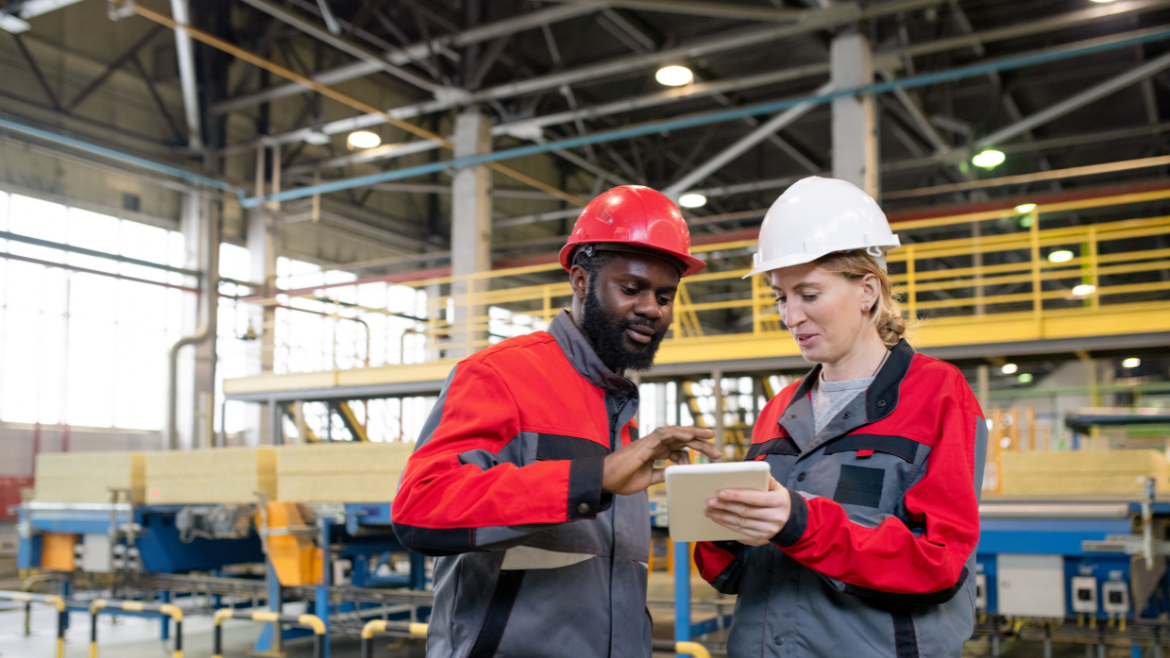
In 2011, German engineering and technology company Bosch changed the world of manufacturing forever.
At its country’s Hannover Messe industrial fair, the company introduced a then-groundbreaking concept: integrating manufacturing with modern information and communication technologies. That new concept ushered in a new age: Industry 4.0.
Also known as the Fourth Industrial Revolution, Industry 4.0 has brought many gifts to manufacturers. It’s given us cloud computing and the Internet of Things (IoT). Massive advances in automation and robotics. Real-time data collection and analytics. 3-D printing, Artificial Intelligence (AI), machine learning, and more.
These smart technologies have increased efficiency and cost savings, enabled greater flexibility and customization within factories, improved product quality, and optimized supply chains.
But for whom?
Factions of the Fourth Industrial Revolution
According to a 2023 report by the Organisation for Economic Cooperation and Development (OECD), large manufacturing companies are leading the deployment — and reaping the benefits — of Industry 4.0 technologies.
Research shows that small to mid-sized manufacturers (SMMs), on the other hand, lag considerably.
If you’re the leader of an SMM today, you probably don’t need to read the recent Information Technology and Innovation (ITIF) report to guess why. Larger manufacturing companies simply have more financial and human resources to invest in Industry 4.0’s rapidly advancing and expensive technologies.
This doesn’t mean you should pack up your manual CNC machine and call it quits. Instead, we recommend tackling the most common barriers to joining the revolution by thinking creatively and economically. Here are the three most common Industry 4.0 challenges SMMs face today — and some of the solutions we’ve helped our client SMMs implement.
The Challenge: Cost Barriers
Implementing Industry 4.0 technologies can be expensive, making it challenging for smaller manufacturers to keep up with competitors.
The Solution: Don’t assume you need to transform your plant into a smart factory humming with smart machines and reams of big data to be more competitive. Start small, with a look at your production lines, how you handle logistics and supply chains, and any data analytics processes you have (or would like to have) in place.
Carefully evaluate those current processes to identify areas where new technologies could make the most significant impact. Prioritize implementation according to budget, and once any technology or new process is implemented, monitor progress. This approach allows for a smoother transition and minimizes the potential disruption to production or other parts of operations. It also allows you to fully assess the impact of each technology before making additional investments.
If your budget is too tight, consider collaborating with another company. Larger and non-competitor manufacturers may be open to sharing resources, expertise, or even access to some form of advanced technology they use. Similarly, partnering with technology providers can give small to mid-sized manufacturers access to specialized software or equipment without making a significant investment.
In addition to looking outside your company for less expensive access to 4.0 tech, look within. Maximizing tax savings can reduce the impact of costs, too. Work with your accountant to determine if you’re taking advantage of available tax benefits or incentives. Doing so might reduce your overall tax liability, freeing up cash flow to invest in technologies that could benefit your business for years to come.
For example, the R&D tax credit allows manufacturers to claim a credit for qualified research expenses related to developing or improving products or processes. This can provide significant tax savings while also encouraging innovation within your company. (What does it take to qualify? Read more here.)
Additionally, accelerated depreciation deductions allow businesses to deduct a larger portion of the cost of qualifying assets in the year they are placed into service. This can offset the initial costs of implementing Industry 4.0 technologies and provide a faster return on investment.
The Challenge: Skills Gap
Adopting new technologies requires a skilled workforce, which can be difficult for SMM’s to find and afford.
The Solutions: Invest in training and upskilling your current employees or seek partnerships with educational institutions to develop a pipeline of skilled workers. Encourage and connect employees to courses where they can obtain industry-recognized certifications. It will enhance their skills and show them that you value them and the work they do — critical to employee engagement.
Research consistently shows that engaged employees are more productive, have fewer accidents, and are less likely to leave their jobs. For instance, a Gallup study found that engaged employees are 17% more productive and experience 41% fewer safety incidents compared to their less engaged counterparts.
Manufacturing Digital reported that engaged manufacturing employees are 70 percent more productive than non-engaged manufacturing workers, and found manufacturing companies with engaged employees have:
- a 78% higher safety record
- 70 % lower employee turnover
- 86% greater customer satisfaction
- 44% greater profitability
Another way to improve workforce skills while engaging your employees? Establish mentorship programs where experienced employees can guide and train newer employees, fostering a culture of continuous learning. Likewise, you can implement cross-training programs to ensure your employees are proficient in multiple areas, increasing flexibility and resilience within your existing workforce.
The Challenge: Tech Integration
Integrating new technologies into existing manufacturing processes can be complex and time-consuming, leading to disruptions in production.
The Solution: Approach any integration process strategically and in phases. Involve stakeholders in the decision-making and implementation-planning process. Work together to create a reasonable timeline that includes specific tasks, “owners” of those tasks, and milestones. Continue to meet and monitor progress, updating the timeline or tasks as necessary.
Your Takeaway
Industry 4.0 presents many challenges for SMMs. But it also offers significant opportunities for better margins and growth though greater efficiencies, productivity, data-driven decision-making, and agile operations. By evaluating your operation’s most pressing needs, forging industry collaborations and partnerships, investing in employee training and engagement, and utilizing tax strategies, you can better afford and manage the challenges of Industry 4.0 and position your manufacturing operation for success in this age of digital transformation.
At Rehmann, we understand the unique challenges facing small and mid-sized manufacturers today. From boosting employee engagement and optimizing tax strategies to implementing cyber-physical systems and helping you grow your business alongside your personal wealth, Rehmann has a team of manufacturing specialists ready to listen and partner. Contact us today or learn more about our specialized manufacturing services here.